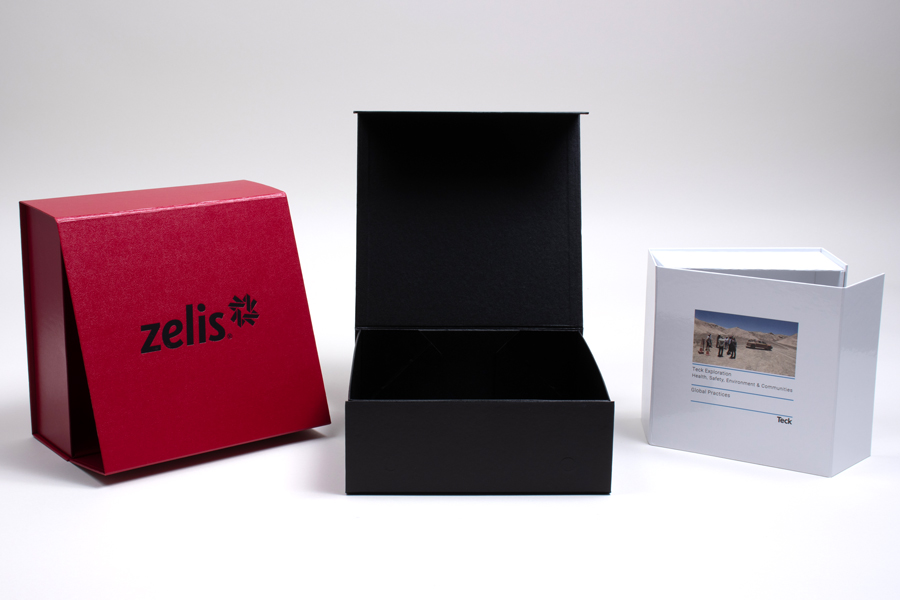
The production of custom magnetic closure boxes requires a meticulous approach, especially when it comes to printing. While these boxes are a popular choice for packaging due to their aesthetic appeal and functionality, various challenges can arise during the printing process. In this article, we will explore five common obstacles that individuals and businesses encounter when printing custom magnetic closure boxes, along with their types and explanations.
Color Inconsistencies
Achieving consistent and accurate colors across different elements of your custom magnetic closure boxes can be challenging. Variations in color can occur due to differences in printing equipment, substrates, ink types, and even environmental factors. Color mismatch or shifts can result in a final product that does not align with your brand’s identity or design intent.To address color inconsistencies, it’s essential to work with a professional printing service that employs color management techniques. This involves using calibrated monitors, color profiles, and regular checks to ensure accurate and consistent color reproduction.
Registration Errors
Registration errors occur when multiple printing plates or colors do not align correctly. This can result in blurred or misaligned text, graphics, or images on your custom magnetic closure boxes. Misregistration can make your packaging look unprofessional and negatively impact the overall quality.Preventing registration errors requires careful pre-press preparation, including proper plate alignment, ensuring that registration marks are well-defined, and employing skilled press operators to monitor and adjust the printing process as needed.
Misregistration and trapping issues are common challenges faced during the printing of custom magnetic closure boxes, and they can significantly impact the quality and appearance of the final product.
Misregistration
occurs when different printing plates or colors do not align correctly. This misalignment can lead to blurred or misaligned text, graphics, or images on your magnetic closure boxes. The result is a packaging design that appears unprofessional and lacks the precision that is essential for creating a polished and aesthetically pleasing presentation. Misregistration can undermine the entire purpose of custom packaging, which is to enhance the visual appeal and branding of your products.
Trapping issues,
on the other hand, refers to problems related to the overlap of different ink colors or elements. When trapping is not managed correctly, it can result in overlapping colors that create unintended and undesirable effects. This can be particularly problematic when working with intricate and multicolored designs. Trapping issues can lead to visual inconsistencies, color bleeding, and a lack of clarity in the printed images on your magnetic closure boxes.
Ink Smudging and Set-off
Ink smudging and set-off can be a significant concern in the printing process. Set-off happens when ink from the freshly printed surface transfers to another surface, leading to unwanted marks and blemishes on your custom magnetic closure boxes. Smudging occurs when the ink does not dry properly or when there’s inadequate drying time between printing and finishing. To prevent ink smudging and set-off, it’s crucial to use the right type of ink and ensure proper drying times. Employing quick-drying inks and suitable drying techniques can significantly reduce the risk of these issues.
Substrate Compatibility Issues
The type of substrate (paper, cardboard, plastic, etc.) you choose for your custom boxes can impact the printing process. Ink absorption, surface quality, and substrate warping are common problems that can affect the final result. If the substrate is not suitable for the printing method used, it can lead to poor image quality and adhesion problems. Choose substrates that are compatible with the printing process you plan to use. Coated substrates often work well for sharp and vibrant print quality. Additionally, considering the substrate’s texture and thickness is crucial to ensuring the ink adheres correctly.
Print Quality Control
Maintaining consistent print quality throughout the production of custom magnetic closure boxes can be challenging. Print defects such as streaks, misprints, or low-resolution images can arise due to various factors, including equipment wear and tear, improper maintenance, or outdated printing technologies. Regular equipment maintenance and calibration are essential to ensure consistent print quality. Investing in modern printing technology and skilled operators can significantly reduce print defects and inconsistencies.
Conclusion
The production of custom magnetic closure boxes involves a complex printing process that can encounter several challenges. Addressing these obstacles requires a combination of advanced equipment, skilled operators, and meticulous pre-press planning. By understanding and proactively mitigating these common printing issues, you can ensure that your custom magnetic closure boxes meet the highest quality standards, effectively representing your brand and enhancing the unboxing experience for your customers.