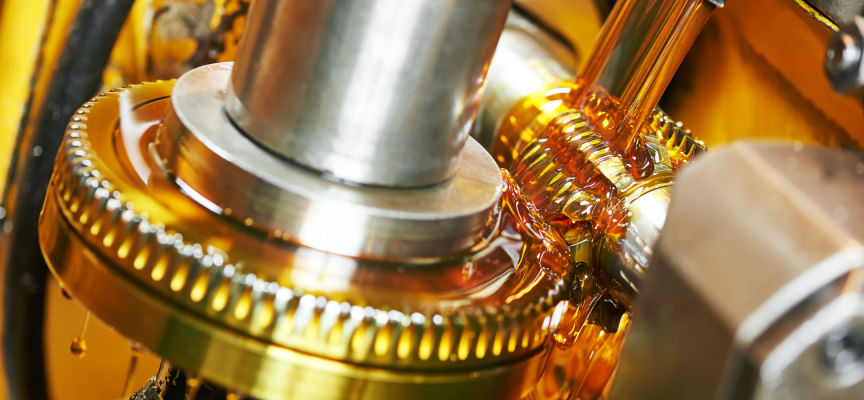
In the realm of industrial machinery, the longevity and efficiency of equipment heavily rely on proper and consistent lubrication. Over time, the advancement of technology has brought forth a crucial solution in the form of automatic lubrication systems.
These systems are a game-changer in the maintenance of heavy machinery, ensuring that critical components receive the necessary lubrication at precise intervals, reducing wear and tear while optimizing operational efficiency.
Unveiling the Automatic Industrial Lubrication System
Automatic lubrication systems are sophisticated mechanisms designed to deliver precise amounts of lubricants to various machinery parts automatically. These systems are used across a wide spectrum of industries, including manufacturing,
construction, mining, automotive, and more, where continuous and accurate lubrication is pivotal for smooth operation.
Components and Functionalities
1. Pump Unit: The core of the system, the pump unit, is responsible for transferring the lubricant from the reservoir to the specific lubrication points
within the machinery.
2. Reservoir and Distribution Lines: The reservoir holds the lubricant, and a network of distribution lines carries the lubricant to individual points requiring lubrication.
3. Control System: Many modern systems incorporate sophisticated control units, allowing programmable features that regulate the flow rate, intervals, and quantity of lubricant dispensed to suit specific machinery requirements.
4. Monitoring and Feedback Mechanisms: Some systems come equipped with sensors or monitoring devices that offer feedback on the lubrication process, alerting maintenance teams about potential issues or the need for refills.
Advantages of Automatic Industrial Lubrication Systems
The adoption of automatic grease lubrication systems offers an array of advantages that significantly impact machinery performance and maintenance:
Precision in Lubrication
These systems ensure consistent and accurate delivery of the right amount of lubricant at the right time, avoiding both over-lubrication, which can cause inefficiency and environmental issues, and under-lubrication, which leads to machinery breakdowns.
Increased Machinery Longevity
Proper and timely lubrication is directly linked to the lifespan of equipment. Automatic systems provide the right amount of lubrication at regular intervals, reducing wear and tear and extending machinery life.
Enhanced Efficiency
By automating the lubrication process, these systems free up human resources for other crucial tasks, boosting overall productivity and reducing downtime associated with manual lubrication processes.
Cost Efficiency
While the initial setup of automatic lubrication systems might require an investment, the long-term cost savings are substantial due to reduced maintenance and repair expenses, and increased operational efficiency.
Factors Influencing System Selection
When choosing an automatic industrial lubrication system, several factors should be considered:
Type of Machinery and Lubricant: Different machinery types have specific lubrication needs. Understanding these requirements is essential for selecting the appropriate system and lubricant.
Environmental Conditions: Some systems are built to withstand extreme temperatures, humidity, or other environmental factors, a crucial consideration for certain industries.
Maintenance and Care
Regular maintenance is vital for the optimal performance of automatic lubrication systems:
Scheduled Inspections: Regular checks for leaks, proper functionality of pumps, and any irregularities in the lubrication process are essential.
Refilling and Replenishing: Ensuring the reservoir is adequately filled with the appropriate lubricant to prevent interruptions in the lubrication process.
Conclusion
The automatic lubrication system stands as a testament to technological advancements in machinery maintenance. By providing precise and consistent lubrication, these systems play a pivotal role in enhancing machinery efficiency,
longevity, and cost-effectiveness. Selecting the right system, understanding machinery requirements, and regular maintenance are key in reaping the full benefits of this transformative technology. As industries continue to evolve, these systems will undoubtedly remain a cornerstone in the realm of machinery maintenance and operations.