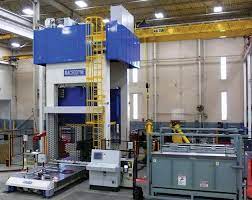
Hydraulic presses generate and transfer force by using hydraulic fluid. They use a pump and hydraulic accumulator to create high-pressure fluid.
There are few manufacturing technologies stronger than a hydraulic press. They are used across a wide range of facilities to aid in fabrication, assembly and maintenance operations. Hydraulic presses are easy to set up and operate. Understanding how they work is essential to their utility.
How They Work?
A hydraulic press utilizes the fundamental hydraulic principle outlined by Pascal’s Law to generate force and pressure. This principle states that any change in pressure on an incompressible fluid within a closed system is transmitted undiminished to all points and acts at a right angle to the enclosing walls.
High-pressure hydraulic oil is stored in a reservoir connected to the hydraulic cylinder. When a machine operator activates the hydraulic pump, it pumps the oil into a smaller piston in a larger cylinder. This creates pressure, which is transferred to the ram. This translates into a substantial mechanical force that can crush materials like wood, metal, and plastic. A hydraulic presses ability to magnify a small mechanical input into a considerable output is what makes it so useful for many applications.
Cylinders
If you have ever seen a piece of heavy machinery like a crane, it is likely that there are hydraulic cylinders positioned all over it. These convert pressure into movement by pushing or pulling on a piston rod that is attached to the machine component the cylinder is interacting with.
Cylinders are usually built out of strong steels to withstand the hydraulic fluid pressure that they hold inside. They have ports that hydraulic fluid moves in and out of to retract and extend the piston rod. The rod is a hard chrome-plated piece of cold-rolled steel that connects to the piston and extends from the cylinder’s rod end head. The outer surfaces are fabricated with seals that are slow to wear and are made from a variety of materials, depending on the application.
Reservoir
The reservoir is a large container that holds the hydraulic fluid for the entire system, including a reserve to cover losses from minor leakage and evaporation. It is mounted above the pump and motor on a base frame to provide easy service access to the system components. It also provides flooded suction for the pump and features a baffle between the return lines to force returning oil back into the tank. This helps reduce contamination by releasing air entrained in the fluid into the tank environment.
The reservoir is usually constructed from a strong, corrosion-resistant material. It is usually fitted with a strainer, drain plug and a way to monitor fluid level, such as a direct reading sight gauge or a clear tube.
Pressure Gauge
For hydraulic systems, the gauge is a key tool for managing pressure levels. Incorrect management of these systems could lead to a loss of efficiency or even physical harm to system operators.
Vibration and pulsation in the hydraulic system cause the pointer on a gauge to bounce rapidly back and forth, making it difficult for an operator to read the reading. This is known as “pointer flutter” and can also result from equipment such as pumps or valves turning on and off at high speeds, creating a sudden pressure spike. Gauges for low pressures (under 600 mbar) use a capsule pressure sensor which is made of two wavy Teflon diaphragms welded together at their periphery and sealed into one container. The sensor can be filled with glycerine or optical silicone to improve its operation and lifespan.