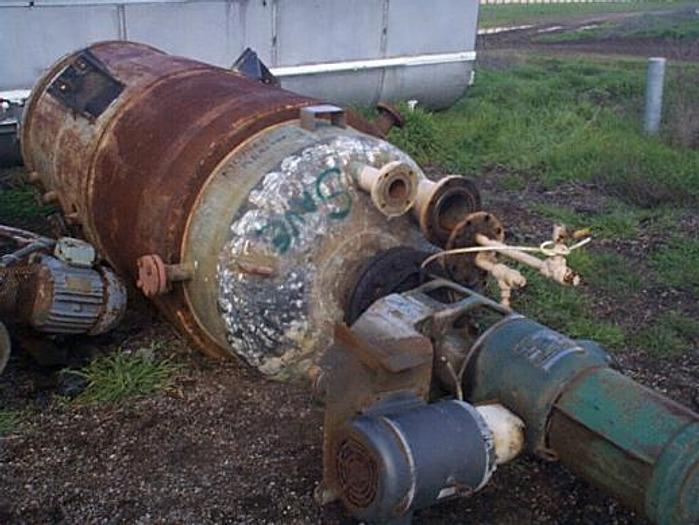
Reactors where chemical reactions occur, differ from small tubes and flasks utilized in laboratories to huge structure like kilns and kilns designed to create lime. Reactors can also be classified as batch or continuous.
The batch process reactors comprise the simplest types. They are made up of a tank equipped with an agitator, and also an ability to either heat or cool the reaction.
Chemical reactors Comprise
Chemical reactors are utilized for industrial processes, converting substances into a final end product. Reactors are developed by chemical engineers and can range in size from a tiny amount of cubic meters, to enormous structures depicted in photographs of industrial plant structures including kilns which create cement using limestone, or the oxygen-based cracking procedure in the production of ethylene oxide (Figure 1.).
There are two types of chemical reactors: batch and continuous. Continuous reactors let the system to reach an unchanging state of operation, whereas batch reactors can’t. A semi-batch is a reactor that uses both batch and continuous inputs and outputs. Semi-batch operations are when a reaction is added to the reactor with a batch of reagents. It is then continuously eliminated to produce a final product, for example as a gas or solid.
The very best chemical reactors are designed to enhance the output of the desired chemical, but keeping the outlet and inlet degrees of conversion within an acceptable of. This goal requires the consideration of multiple trade-offs, such as the proportions of size and the conversion of reactants, or the balance of heating transfer surface and hot spot temperature. The issue is solved effectively using multi-objective optimization techniques.
The latest development of chemical reactors design is the use of advanced analysis and optimization tools in order to find the most efficient types of chemical reactors to use for particular processes. The tools use thermodynamics, mass transfer correlations as well as kinetics, to maximize your reactor as part of the entire process framework through simultaneous identification of the most effective reaction idea and optimum process design parameters.
Buy Reactors Desired
Chemical reactors chemical reactors is a process machine that allows chemicals to be fed into the system to make their reactions in order to create a desired product. Reactions can be observed throughout a wide range of industries like polymer industries, the dyes and pigments industry, color industries etc.
Reactions may be continuous or in a batch. It is possible to batch buy reactors are closed systems in which a batch of reactants is placed in the reactor all in one go and reaction permitted to happen in just one process. The reactants then are removed and the reactor cleaned ready to be used for the next batch of reactionants which will then be added. One advantage of a batch process in comparison to continuous processes is that it has lower expenditure on capital.
The second sort that comes with chemical reactors is called a continuous stirred tank reactor (CSTR). These are open-systems that allow the reactants to continuously are pumped into and out the reactor. As opposed to the batch, that can be used reactors in either liquid or gas phases, CSTRs are specifically designed to function in both. These are also called tubular reactors due to the fact that they consist of a tube-like vessel which the reaction happens. In this type of reactor, a control rod could be inserted into the reaction for reducing the speed of reaction or pulled out to increase the rate of reaction. The size that the process is, these types of reactors can be employed in liquid or gas phase systems.
Industrial Reactors Fuel Efficiency
A variety of chemical reactions that are used in industries happen in industrial reactors which range from the small test-tube and flask used reactors for experiments in chemistry labs to the vast structures depicted in photographs of industrial facilities. The main types are batch process reactors that put in the reactants, permit reactions to occur and finally release substances, and then continual process reactors, which are able to be run for long periods without shutting down.
In this case, for example, the carbon monoxide that is produced through the combustion of natural gas in a boiler will be continuously transformed into the liquid form (butane) by a catalytic cracker. Gases flow over a bed composed of a solid catalyst (typically silica-alumina) in which the material has been heated to very high temperatures to extinguish the carbon. The temperature of the gases is controlled by regulating the pressure of the air by means of one of the valves.
A different type of reactor is the fluidized bed reactor which uses finely ground catalyst particles to be suspended in hot gaz (often steam) which flows over the particles. This gives excellent mixing of the reactants with a very big surface area. It also allows heat to be transferred rapidly from the catalyst to reaction mix. They are particularly useful in exothermic reactions like the nitration of aromatic hydrocarbons. They can also be explosive.
Aaron Equipment offers a large assortment of reconditioned, used industrial reactors for sale including glass lined, carbon steel and alloy reactors built to work with materials that are corrosive. They are industrial reactors are ideal for commercial applications such as mixing of product, solids dissolution, extraction of liquids and distillation on a batch.