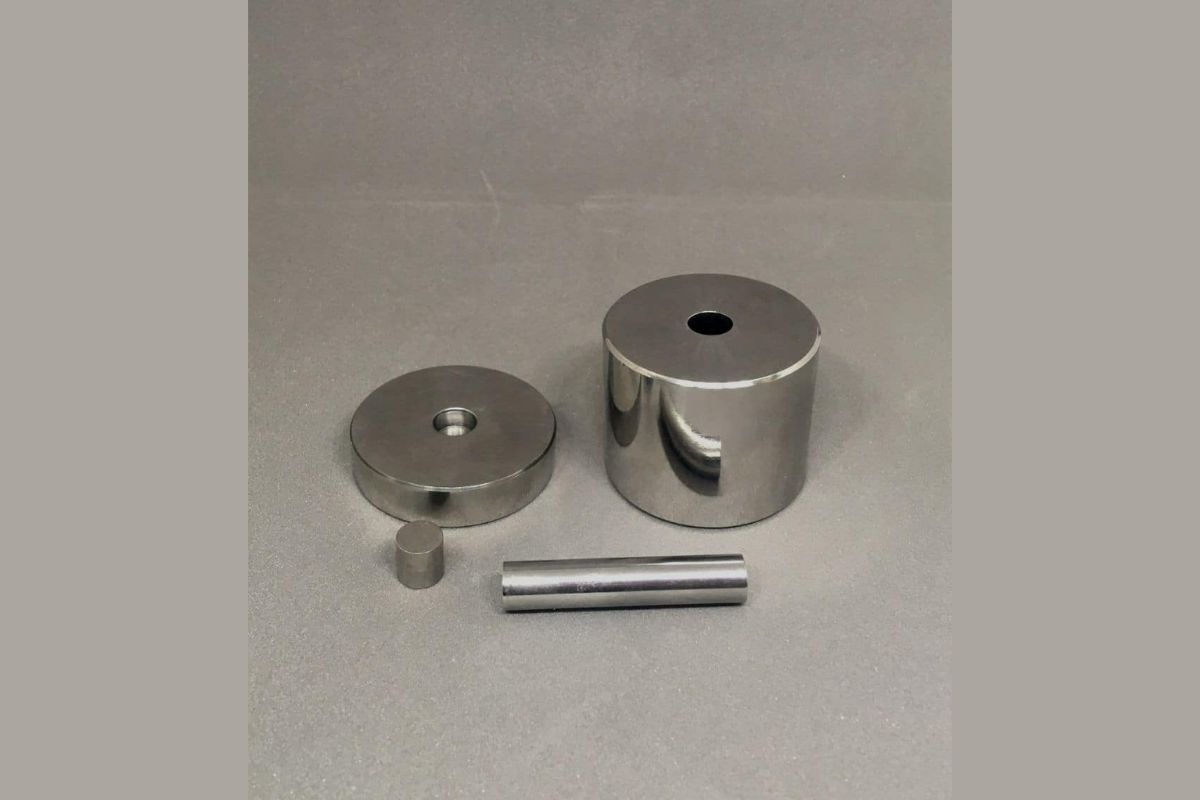
Choosing the right pellet press die set material is a complex process. There are many factors to consider including ingredients, conditioning moisture and temperature, and die specifications.
Flat die pellet mill has simple structure and is light, small and portable. It is also easy to operate and maintain. This type of pellet machine can make high-quality pellets.
Die Material
In order to produce pellets with a high level of quality, your pellet mill relies on the die set that you use. There are several factors that must be taken into consideration when selecting the right die set, such as hole specifications, compression ratio, and relief design. Choosing the wrong specifications can lead to poor pellet quality or increased maintenance costs.
A typical pellet press die set is fabricated from a metal such as tool steel, carbon steel, or stainless steel. The material determines the cost and durability of the die set, with stainless steel being the most expensive but also the longest lasting. Carbon steel die sets are less expensive but tend to wear down faster than stainless steel. In addition to the material of the die, the hole size and the compression ratio also impact how long the pellet press die set will last.
Our EQ-Va-Die is made from a high quality grade of stainless steel that is annealed and then precision ground for perfect dimensional compatibility with all Chemplex(r) stainless and tungsten carbide pellets as well as PelletCup(r) compressible tapered aluminum briquetting cups. Stainless steel dies are more resistant to corrosion than their mild steel counterparts, and they will hold up under a lot of pressure, meaning they can be used a longer time before needing replacement. Be sure to clean your die set thoroughly with absolute ethyl alcohol after every use and store in a dry box with silica gel to help prevent surface corrosion.
Compression Ratio
The compression ratio of the pellet press die set determines how much force is needed to push the feed through the hole. The higher the ratio, the more energy is required. Keeping the ratio as low as possible is best for reducing the amount of friction and energy required.
Choosing the correct die thickness is another important factor. This is determined by the raw material being pressed. Typically, thicker raw materials require lower compression ratios as they are harder to mold. For XRF spectrometer applications, the dies must be thick enough to form a metallic ring around the sample for clasping by automated sample handling systems.
A good quality hydraulic lab press is a must for proper pellet pressing. Choose a model that has an accurate pressure gauge so you can know exactly how much force is being used. This will help you prevent damage to the press and the dies while ensuring that your pellets are properly formed. Also, look for a model with an emergency stop switch to protect yourself in the event of accidental activation. Lastly, keep your dies in a dry environment and apply oil mixture to the interior surface to reduce corrosion. This will also help to keep them lubricated and running smoothly. Also, be sure to clean the dies after every use.
Die Thickness
The thickness of die is very important because it determines the overall compactness & PDI (Pellet Durability Index) of the pellet. Thicker dies will have higher compactness & better PDI while thinner dies are more flexible & have lower PDI. The thickness of the die is also dependent upon the feed formulation as more friction between the pellet & the die will wear the die more than less friction between the pellet & the die.
The life of the die set is also dependent on the characteristics & properties of raw materials used in production, like marble powder/silica abrasive particles wear the dies more rapidly than those with good fat content as the fat acts as a lubricant between the pellet & the die. The feed chemistry should be consistent to get good die life.
Whether you are taking a geological sample out of the ground, making metal samples for XRF or trying out new material on your space rocket nozzel, a pellet press is needed to convert that clump of powder into a solid form that can be handled and tested. These professional briquetting presses are used in universities, research centers, big pharmaceutical firms and small businesses around the world. They are also great for briquetting metal powders into a compact form for XRF analysis. Using the right die sets will help you get the best results for your project and minimize downtime due to faulty or worn dies.
Die Relief
When choosing a pellet die set you must be aware that there are many factors to consider when selecting the right specification. Ingredients, conditioning moisture, temperature and pressure are a few of the most important variables, but there are also other specifications that need to be considered, such as the material used for the die, hole specifications, compression ratio and relief design.
When it comes to the material for a pellet press die set, there are two main needs that drive most selection decisions: pellet quality and throughput. The best way to achieve both goals is by using the highest compaction force that can be achieved safely and with good quality. However, the higher the compressive stress that is applied to the powder, the more it can deform or even crack on release.
Fortunately, these forces can be reduced by using low pressing forces and lubricating the die. Also, by limiting the maximum load on the pellet die set to well below the yield stress of the steel, you can avoid any unnecessary or excessive stress on your powder compact. To further reduce the amount of force required for compaction, there is a process called neutral hardening which results in a consistent hardness throughout the die. This type of steel, such as Kingman Chrome Plus, is more durable than conventional case carburized steels.
Read More: Resorbable Fixation