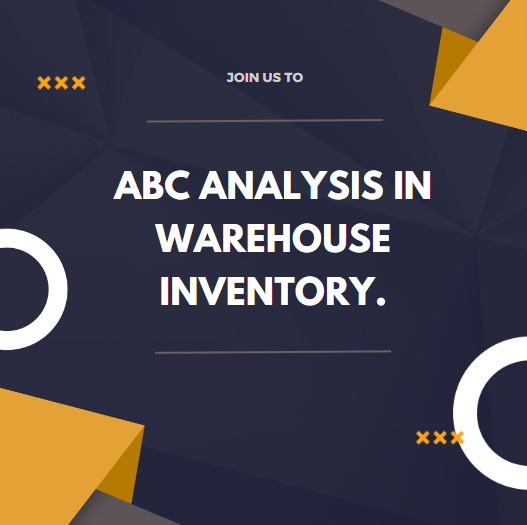
Introduction
In the dynamic world of warehouse inventory management, finding efficient strategies to handle and prioritize stock can be the key to success. One such valuable technique is ABC analysis, which categorizes inventory into three groups based on their importance and value. This method, named after the first three letters of the alphabet, allows businesses to allocate resources effectively, streamline operations, and maximize profitability. In this article, we will delve into the concept of ABC analysis and explore its significance in warehouse inventory management.
Understanding ABC Analysis
ABC analysis is a strategic approach that classifies inventory items into three categories: A, B, and C, each representing a different level of significance to the business.
Category A: High-Value Items (20%)
- Category A includes high-value items that contribute significantly to the business’s revenue. Though they represent only a small percentage of the total inventory, they hold great financial importance.
Category B: Moderate-Value Items (30%)
- This Category comprises items with moderate value and contribute to a reasonable portion of the revenue. They are essential but not as critical as Category A items.
Category C: Low-Value Items (50%)
- Category C includes low-value items that represent most of the inventory but contribute the least to the overall revenue. While individually, they may not hold much value, collectively, they form a significant portion of the inventory.
Implementing ABC Analysis.
Data Collection and Analysis
-
- Begin by gathering data on your inventory, including item costs, demand patterns, and sales history. Analyze this data to determine the value and importance of each item.
Segmentation and Classification
-
- Using the Pareto Principle (80/20 rule), categorize items into A, B, and C groups based on their contribution to revenue. Category A items typically constitute about 20% of the inventory but contribute 80% of the revenue.
Inventory Dominion Policies
-
- Tailor your inventory control policies to each Category. For Category A items, implement stricter controls and monitoring to avoid stockouts. Category B items may require regular monitoring, while Category C items can follow a more relaxed approach.
Resource Allocation
-
- Allocate resources, such as storage space, workforce, and technology, based on the importance of each Category. Category A items may warrant prime storage locations and advanced security measures.
Benefits of ABC Analysis in Warehouse Inventory Management.
Enhanced Prioritization
-
- ABC analysis clearly focuses on high-value items, ensuring that critical stock is always available to meet customer demand.
Efficient Resource Utilization
-
- By allocating resources proportionally to the importance of each Category, businesses can optimize space, labor, and capital investments.
Cost Reduction
-
- Category C items, which comprise the largest portion of the inventory, can be managed with more cost-effective strategies, helping minimize expenses.
Improved Forecasting and Planning
-
- ABC analysis provides valuable insights into demand patterns and allows for more accurate forecasting, aiding in procurement and production planning.
Conclusion
Implementing ABC analysis in warehouse inventory management can be a game-changer for businesses seeking to optimize operations and boost profitability. Businesses can make informed decisions regarding resource allocation, inventory control policies, and overall operational strategies by strategically classifying items based on their significance. Embracing this method empowers businesses to stay competitive in a rapidly evolving market, making it a cornerstone of modern warehouse management practices.