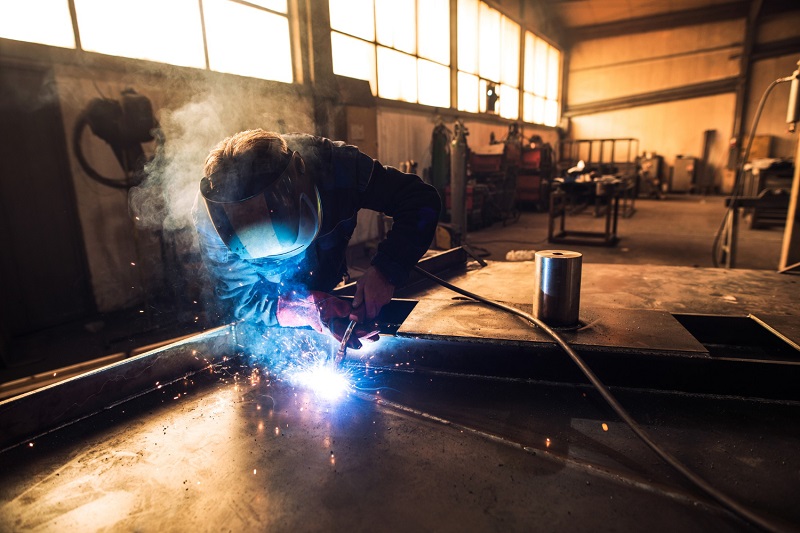
In MIG (Metal Inert Gas) welding, shielding gas is a critical component that greatly impacts weld quality and properties. While the continuously fed wire electrode and constant current arc do the actual welding, the shielding gas plays an equally vital role. This inert gas protects the weld pool and controls the atmosphere during welding. Without proper shielding gas, a MIG weld would be riddled with defects and almost unusable. In this article, we’ll examine why Mig welder gas is so important for good mig welding results.
How Shielding Gas Works In MIG Welding
As the name indicates, the shielding gas provides a protective shield around the arc and molten weld pool. This displaces air, preventing it from interacting with the weld as oxygen can severely compromise the chemical and structural integrity. Specifically, the shielding gas:
- Displaces oxygen and nitrogen to prevent oxidation – Oxidation causes porous, brittle welds with excess spatter.
- Cools the weld area after the arc passes – This controls the weld’s shape, appearance, and penetration.
- Shapes the characteristics of the arc – This impacts how smoothly the arc transfers from the wire to the workpiece.
- Affects metal transfer mode – Spray, globular, short circuiting, and pulsed spray transfer rely on the gas used.
Without this shielding effect, welds become choked with inclusions and voids making them hazardous to rely on in any application.
Gas Selection Impacts Weld Properties
MIG shielding gases are inert, meaning they do not react with the molten metal. The most common options are pure argon, pure CO2, and argon/CO2 mixes. Choosing the right gas or blend is critical as it impacts:
- Penetration – Higher CO2 increases penetration while high argon gives a shallower weld. Blends tune penetration as needed.
- Bead profile – More CO2 flattens and widens the weld while argon produces a higher, narrower convex bead.
- Mechanical strength – Argon-rich mixes yield stronger welds while CO2-rich mixes are hotter and faster.
- Metallurgy – Gases affect the transition between solid and liquid metal, modifying the weld composition.
- Oxidation resistance – Argon provides the best oxidation protection for steel and metal alloys.
- Cost – 100% argon is most expensive while CO2 is lowest cost. Mixed gases balance cost and performance.
Proper Flow Rate And Nozzle Positioning
The flow rate and nozzle position also greatly influence shielding gas effectiveness. Too low of a flow rate allows oxygen to contaminate the weld and increases turbulence. Excessively high flow blasts away the shielding envelope.
The nozzle must be positioned to direct shielding gas right to the weld area. Improper torch angle or distance can leave sections of the weld unprotected. Tuning both parameters takes practice.
For quality MIG welding, precision gas delivery is mandatory. Investing in a MIG welder with accurate gas controls really pays off. Consistency is key for controlling the welding atmosphere.
Optimize Shielding Gas Coverage With Welding Fume Extraction
Proper shielding gas delivery is critical for defect-free welds, but turbulence can disrupt coverage and lead to porosity and other issues. Strategically positioned welding fume extractors from the industry leader Translas create stable, laminar airflow around the weld site that shapes the shielding gas into a protective cone. This prevents crosswinds and drafts from interfering with shielding gas and enables optimal coverage. Translas extraction systems also filter and recirculate clean air to further stabilize the weld atmosphere. For the best shielding gas results, trust Translas fume extractors designed to capture harmful smoke while improving shielding gas protection.
Don’t Compromise On Shielding Gas!
While it’s invisible, shielding gas is at the heart of any MIG weld. Sacrificing on flow rate, coverage, or gas quality is never worthwhile. Professionals never try welding without gas or skimp on protection to cut costs.
Take the time to understand your shielding gas options and how to optimize settings and positioning. With proactive shielding gas management, you can achieve repeatable, high-strength, spatter-free MIG welds every time!